Integración de las válvulas de control a la gestión de activos
ARTÍCULO |Nicolas Palermo, Ing, Consultor de Confiabilidad & Gestión de Activos
“La medición principal de un instrumento de campo inteligente representa el 3% de los datos. El 97% restante se puede utilizar para la gestión de la salud de los activos.
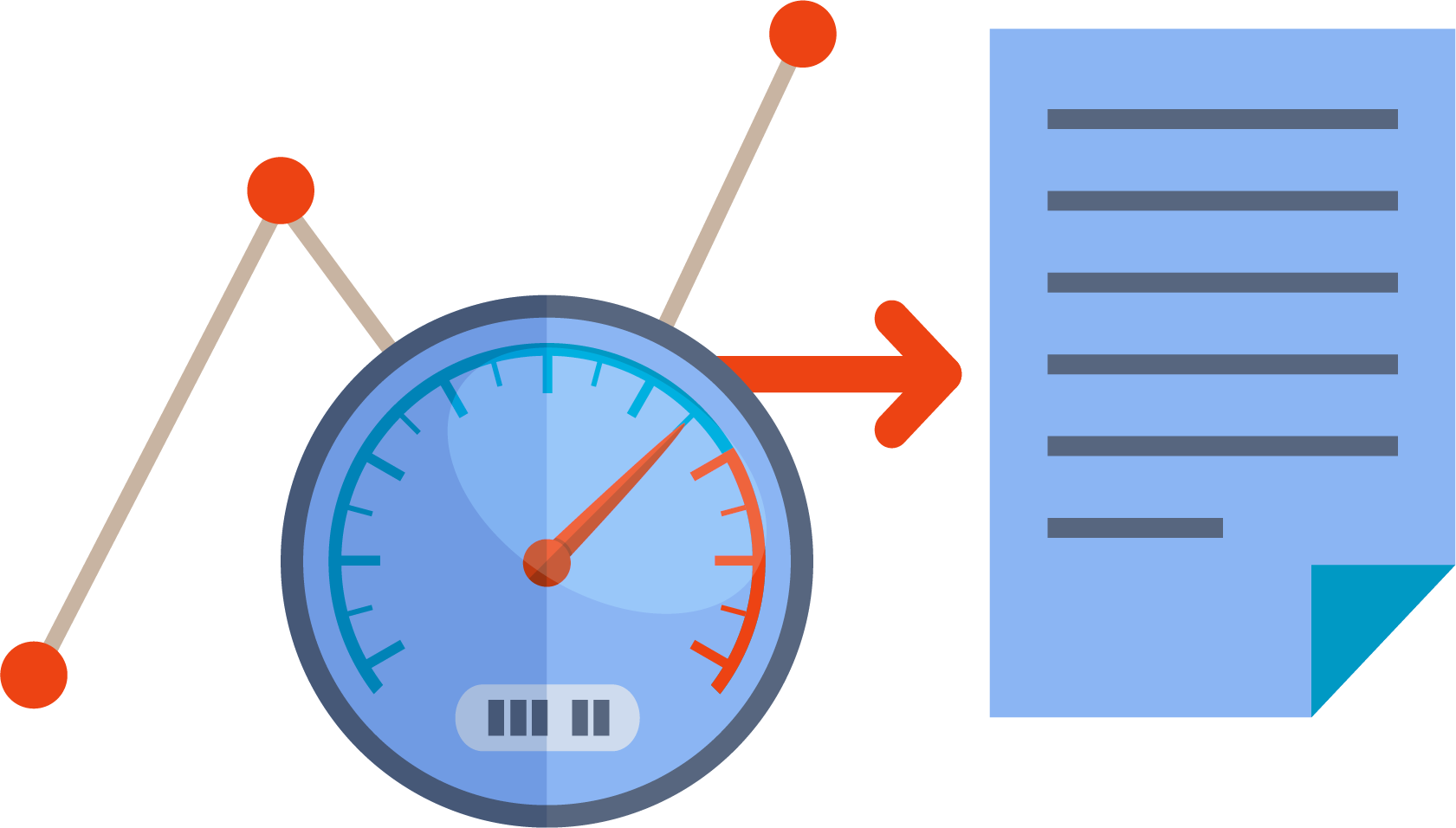
Hace más de 30 años llegaron a los mercados los primeros posicionadores digitales o inteligentes para válvulas de control. Estos posicionadores eran más avanzados y disponían en su parte electrónica de microprocesadores que incorporaron el protocolo de comunicación HART para comunicarse e interactuar con dichos instrumentos de campo.
La llegada de estos posicionadores digitales permitió, además de contar con instrumentos de tecnología de punta para ese momento, disponer de una serie de ventajas que en principio solo estuvieron enfocadas al tema de “commissioning” o puesta en servicio del lazo de la válvula como tal. Esto permitió, a través de procedimientos mucho más simples, la calibración y entonación del lazo propio de la válvula en pocos minutos.
Típicamente con los modelos predecesores de posicionadores neumáticos o los electro-neumáticos disponibles, le tomaba a los técnicos de instrumentación hasta varias horas de labor para poder lograr alcanzar una respuesta realmente aceptable de la válvula frente a la señal de corriente de 4 a 20mA, proveniente del controlador local, un PLC o DCS, logrando ahorros considerables por concepto de menos uso de H-H’s para esta actividad.
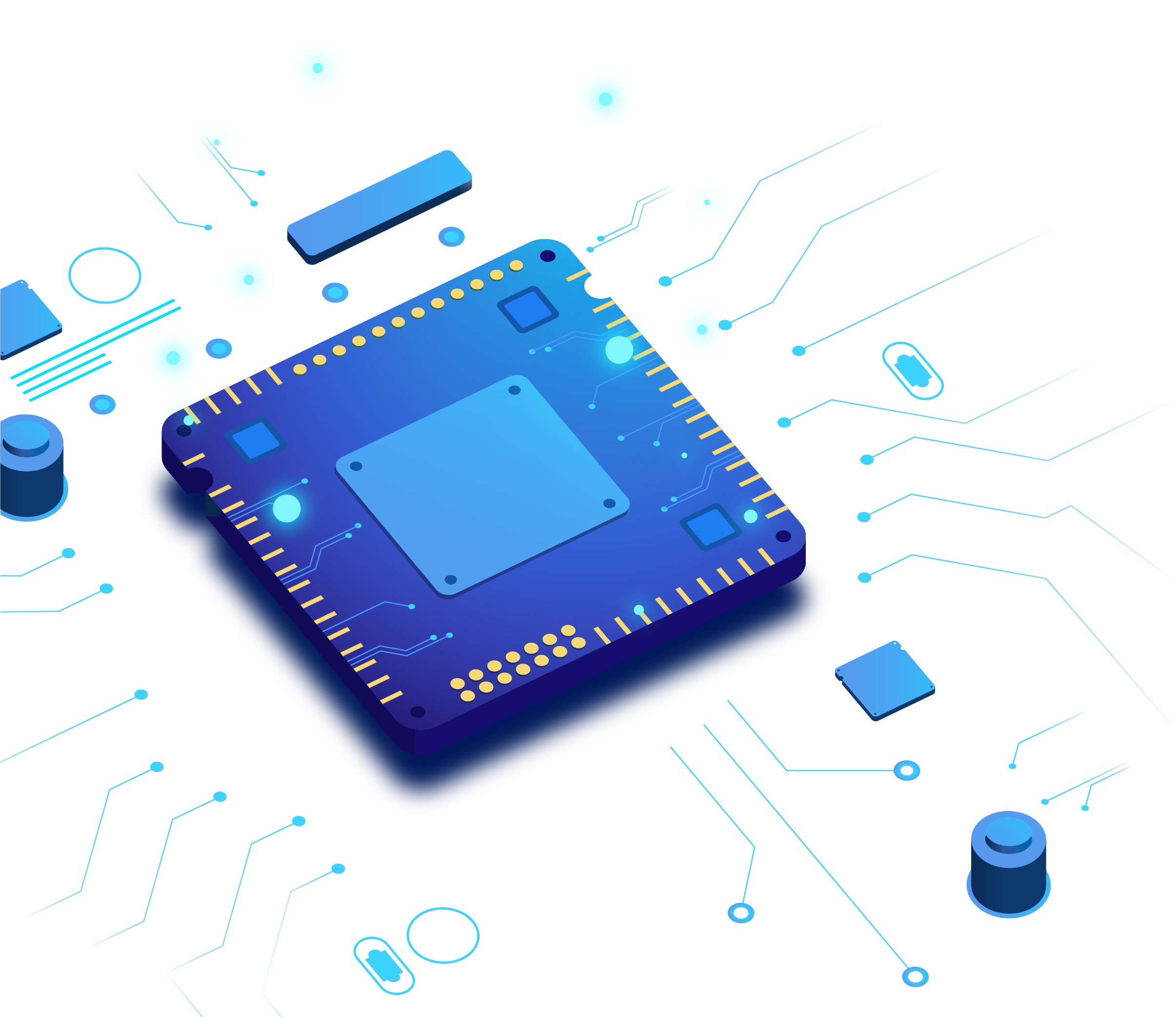
Con el avance del mundo de la electrónica, y particularmente la aparición de procesadores más compactos y poderosos, los principales fabricantes y líderes de este sector de válvulas de control aprovecharon esta situación para ir incorporando a sus equipos mayores prestaciones. Estas prestaciones no solo se limitaban al tema de la puesta en servicio, registrando y almacenando una serie de datos del comportamiento y desempeño no solo del posicionador, sino también de la válvula en la cual se instalarán.
Tales datos desde ese momento han estado disponibles por muchos años en las plantas en las que fue actualizada su base de posicionadores, pero en muy pocos casos esta valiosa información ha sido aprovechada y considerada en su justo valor en la toma de decisiones sobre estos activos de crítica importancia, clave en la calidad y fiabilidad del proceso de la planta o instalación industrial.
Integración de las válvulas de control a la gestión de activos
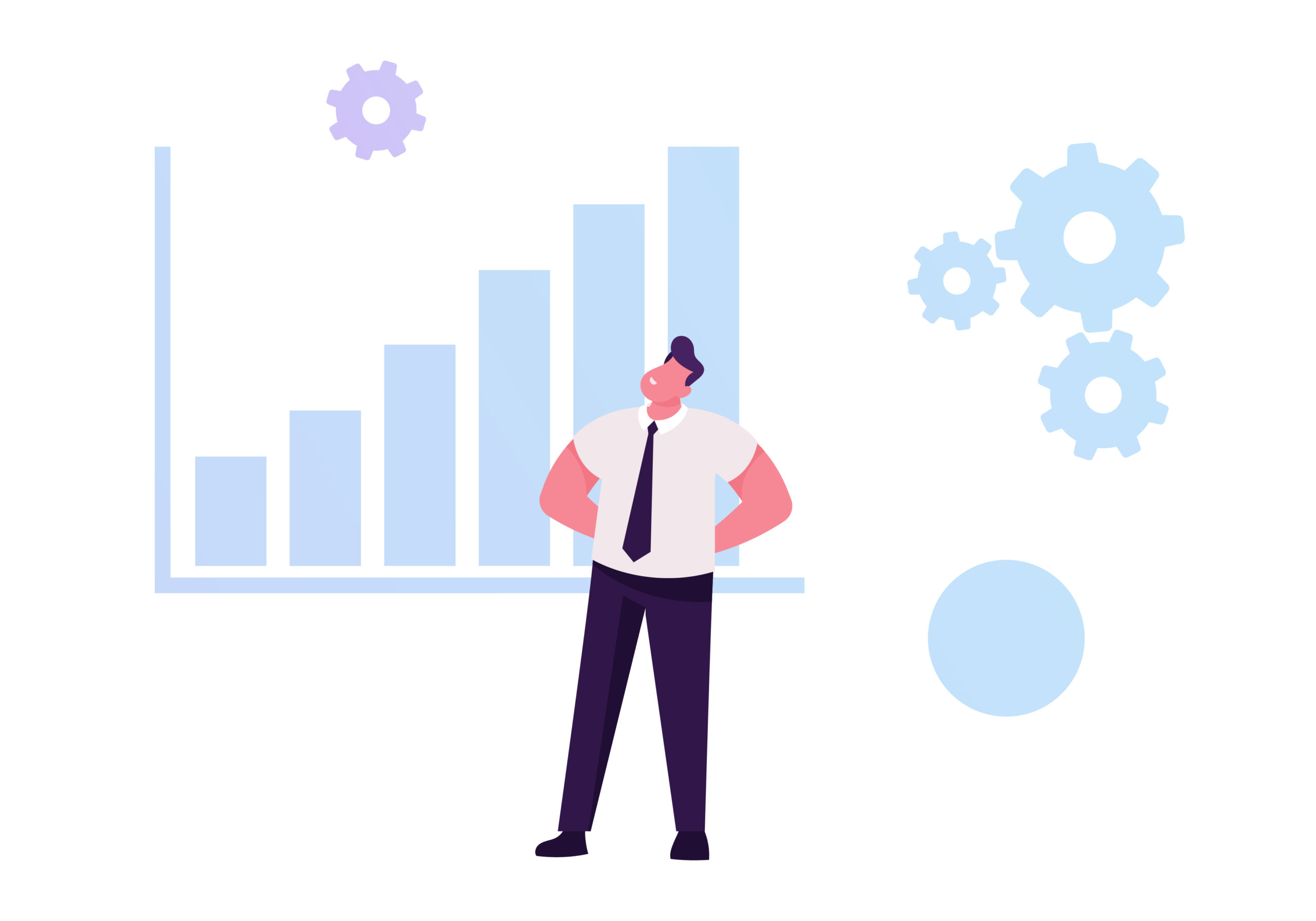
La entrada al mercado y aceptación de los posicionadores digitales no es tema reciente, pero desde su masificación han permanecido en la mayoría de casos como seres “inteligentes” acumuladores de datos. Sin embargo, han estado prácticamente aislados y sin poder compartir, y mucho menos aprovechar, toda esa información con otro sistema jerárquicamente superior que pueda ser de verdadera y máxima utilidad para los usuarios responsables del mantenimiento o de la operación de la planta.
Las plantillas de técnicos de instrumentación han ido ganando y fortaleciendo su experiencia con estos posicionadores. Han logrado bajar considerablemente el tiempo necesario que les toma ponerlos en servicio, bien sea en una instalación de un nuevo equipo luego de un reemplazo por falla o en las pruebas funcionales que se realizan a cada válvula dentro del programa de mantenimiento preventivo durante las paradas de planta programadas.
Sin embargo, hay muchas ventajas y bondades más allá de la puesta en servicio si se extrae, se registra y, sobre todo, se analizan los datos que estos posicionadores proporcionan. Para lograr integrar estos instrumentos y, en definitiva, el lazo de la válvula al cual están asociados, a un sistema de gestión de activos, los ingenieros de confiabilidad de instrumentación pueden ir avanzando por etapas hasta lograr la meta deseada: el monitoreo en línea de estos activos. Esto permitirá a la postre conocer prácticamente en tiempo real la salud de la válvula y la detección de fallas con suficiente anticipación para la toma de decisiones en forma acertada y oportuna.
Optimizando la selección de válvulas que deben ser bajadas o sometidas a un “overhaul” durante las paradas de planta programadas al tomar parámetros basados, no solo en esquemas de tiempo y en el desempeño, sino más bien en la condición que muestra cada válvula.
Esto se traduce en reducciones de entre un 30% a 50% de costos de mantenimiento mayor de válvulas, no solo por los costos inherentes a la reparación o mantenimiento de la válvula propiamente, sino también al no requerir el uso de H-H´s de la cuadrilla de instrumentistas, el desmontaje mecánico, la perdida de aislamiento, construcción y alquiler de andamios o estructuras, servicio de izamiento, transporte hasta y desde un taller externo si fuera el caso, etc.
En esta primera entrega revisaremos que datos o información se pueden obtener de los activos como se muestra en la figura 1. Realizaremos énfasis en los posicionadores digitales en modo “off line” o fuera de servicio y en próximos artículos iremos más allá revisando las opciones disponibles para realizar un monitoreo continuo o en modo “on line” con las válvulas y la planta completamente operativa y sin riesgo alguno.

Figura 1. Sistema automático de captura de datos de los activos (Amendola.L, 2015, 2019)
Cada fabricante ofrece un programa o software que permite comunicarse con mayor o menor facilidad con los posicionadores mediante un dispositivo móvil y desde cualquier punto de conexión del lazo de corriente, bien sea directamente en el posicionador, caja de conexión de señales que van a este dentro de la planta o incluso desde los tableros de entrada/salida de las señales del PLC o DCS. Estos programas básicamente tienen dos propósitos:
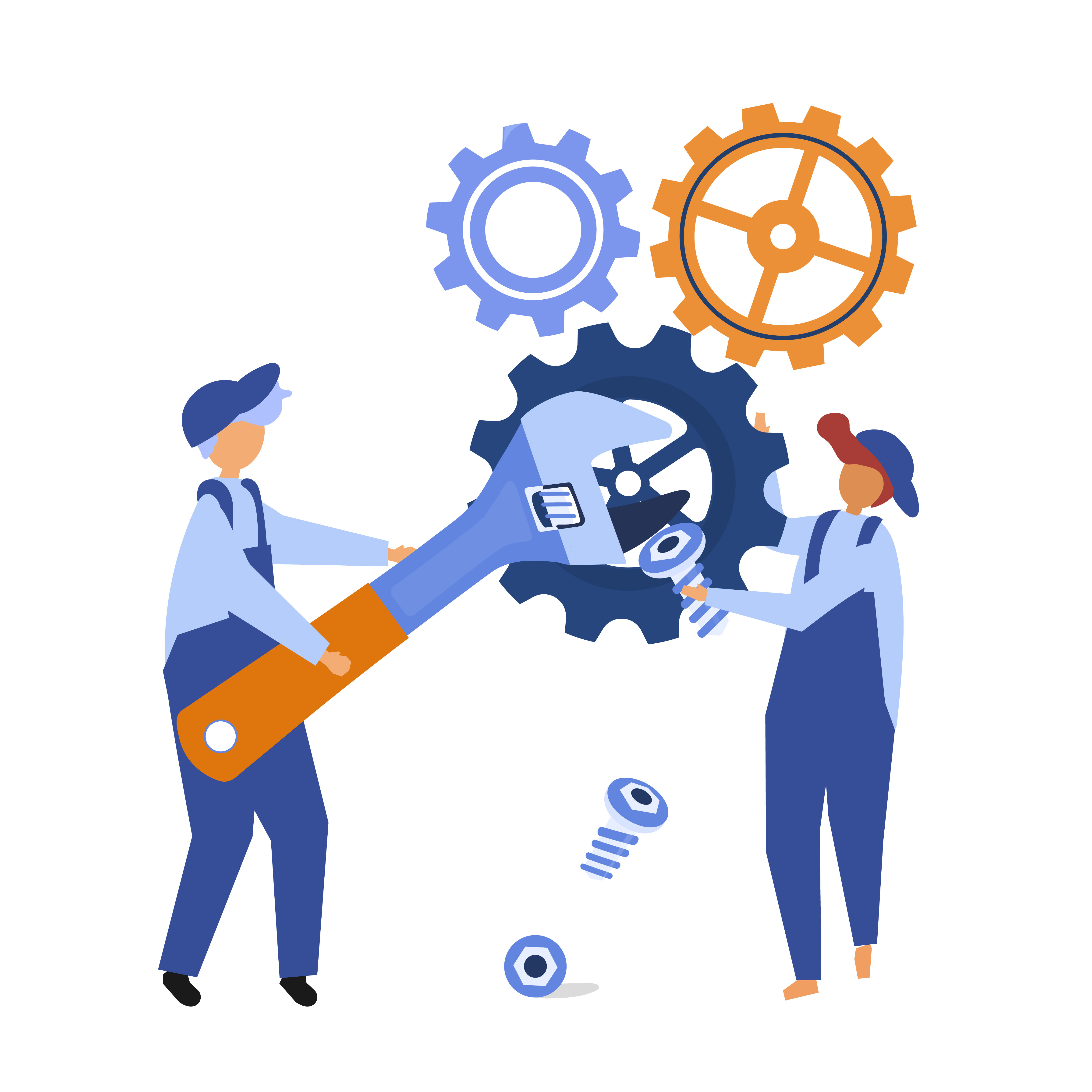
1. Configuración: para preparar y ajustar el posicionador de acuerdo a la válvula estableciendo distintos parámetros como tipo de falla, rango de la señal de entrada, tag o etiqueta, tipo de respuesta (lineal, igual %, apertura rápida, “customizada”) e incluso parámetros PID para la entonación fina del lazo posicionador-válvula.
2. Inspección y diagnóstico: este modo permite conocer la “salud” del posicionador revisando según el fabricante el estado de parámetros propios del equipo como son la temperatura máxima alcanzada en el microprocesador, desconexión o perdida de la señal eléctrica, problemas en el tren neumático, error de posición de la válvula, calibración fallada, etc.
También se puede inferir acerca del estado o salud de la válvula mediante la ejecución de rutinas de diagnóstico que permiten generar y registrar curvas a partir de pruebas típicas como son la “firma” estándar o extendida, respuesta al escalón a la rampa, tiempos de apertura y cierre, etc.
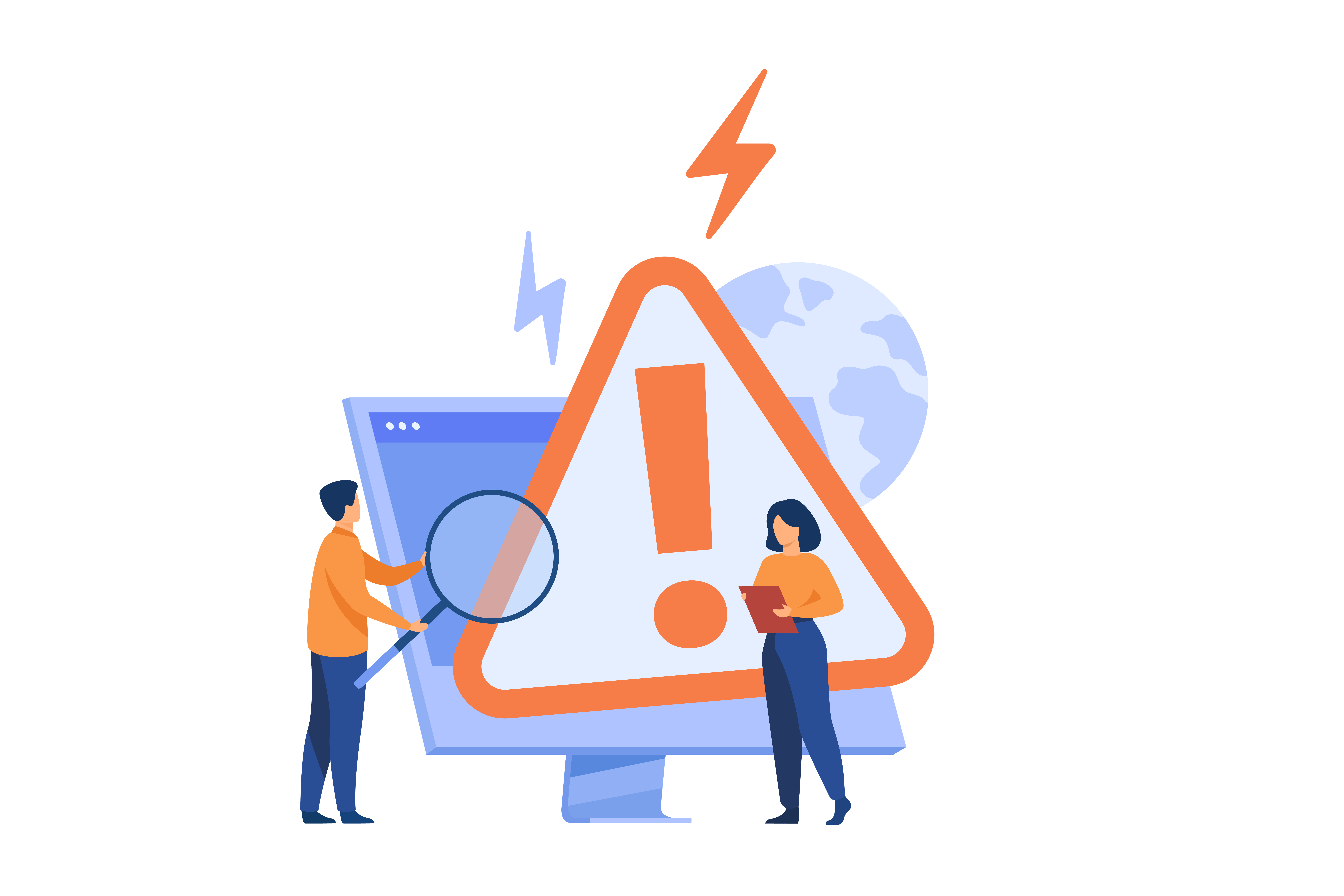
Soluciones de monitoreo del estado de salud de los activos
Los sofisticados dispositivos de campo actuales pueden proporcionar enormes cantidades de datos. Las estimaciones sugieren que la variable primaria básica representa apenas el 3% de los datos que se originan en un instrumento o analizador. Entonces…
¿qué representa el otro 97% de la figura 1?
Naturalmente, varía según el tipo de instrumento: un transmisor de presión diferencial producirá información diferente a la de un caudalímetro coriolis o un actuador de válvula inteligente. Pero en general incluye:
Diagnóstico: indicadores discretos y continuos para estados de problemas internos y fallas aleatorias del sensor y los componentes electrónicos. Estos se pueden indicar de varias formas, incluidas alertas y alarmas. El historial de calibración del dispositivo también reside aquí.
Monitoreo: indicadores continuos de activos y procesos, como el ruido del proceso, que pueden indicar cambios fuera de la función principal de un instrumento.
Detección: variables secundarias, terciarias e incluso adicionales. Estos pueden funcionar individualmente o en conjunto con otros instrumentos para aproximar las mediciones del proceso que no se pueden medir directamente.
La medición principal capturada por un instrumento de campo inteligente representa aproximadamente el 3% de los datos que genera. El 97% restante se puede utilizar para la gestión de la salud de los activos y otros usos.
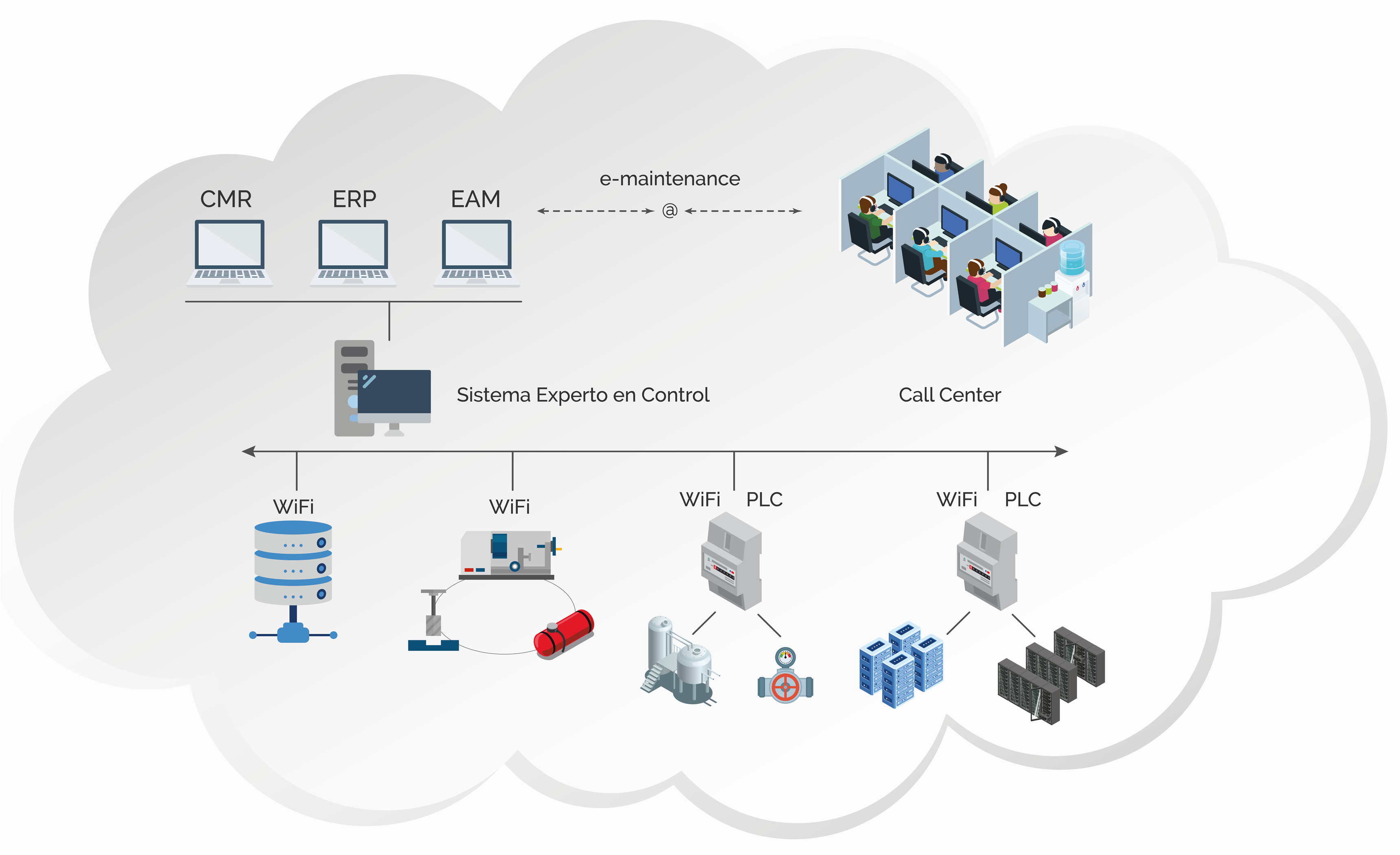
Figura 2. Herramienta de Diagnóstico Salud de Activos (Amendola.L, 2015, 2019)
Una solución de gestión de activos de planta eficaz está diseñada para recopilar los datos adicionales y desbloquear su potencial. Cuando se implementa correctamente, mejorará la disponibilidad y la eficacia de la planta al tiempo que reduce el riesgo de interrupción de la producción, el tiempo de mantenimiento y el esfuerzo.
Beneficios:
– El análisis de datos ayuda a dirigir los esfuerzos de mantenimiento preventivo para ahorrar tiempo, especialmente para dispositivos con altos requisitos de mantenimiento.
– Solución de problemas mucho más rápida, eliminando la necesidad de revisar instrumentos individuales.
– Uso más eficaz del tiempo de los técnicos, ya que pueden comprobar el estado de los instrumentos antes de realizar reparaciones.
– Los datos recopilados y mostrados en paneles para un rendimiento en tiempo real y capturados en historiales para su análisis posterior.
Buenas Prácticas
Si el equipo de confiabilidad de la planta dispone de los recursos y conocimientos, o contrata los servicios de las empresas especialistas o representantes de los fabricantes de válvulas, puede tomar ventaja.
En cada oportunidad o ventana que se presente, bien sea por una parada programada o no, se puede extraer y registrar toda la data que acumula y proporciona el posicionador. Así se pueden realizar los diagnósticos de la respuesta de la válvula a las pruebas de rampa o escalón y acumular estas firmas para ir registrando un histórico que, si bien no es continuo, le permitirá comparar distintos momentos y tendencia de estos parámetros.
Esto servirá para inferir, con la experiencia y conocimientos necesarios, y tomar decisiones asertivas basadas en este comportamiento. Esto ayudará a decidir sobre que válvulas se debe actuar e intervenir y, de esta manera, empezar a manejar planes basados en filosofía de CBM que día a día van demostrando que resultan más efectivos que los planes basados en tiempo de operación o agendados.
Y aunque esta primera etapa no es la guinda del pastel en la confiabilidad de la instrumentación, es un buen inicio del camino a recorrer para poder disponer de técnicas predictivas sobre estos activos que resultan críticos y clave en la calidad y fiabilidad del proceso de la planta o instalación industrial.
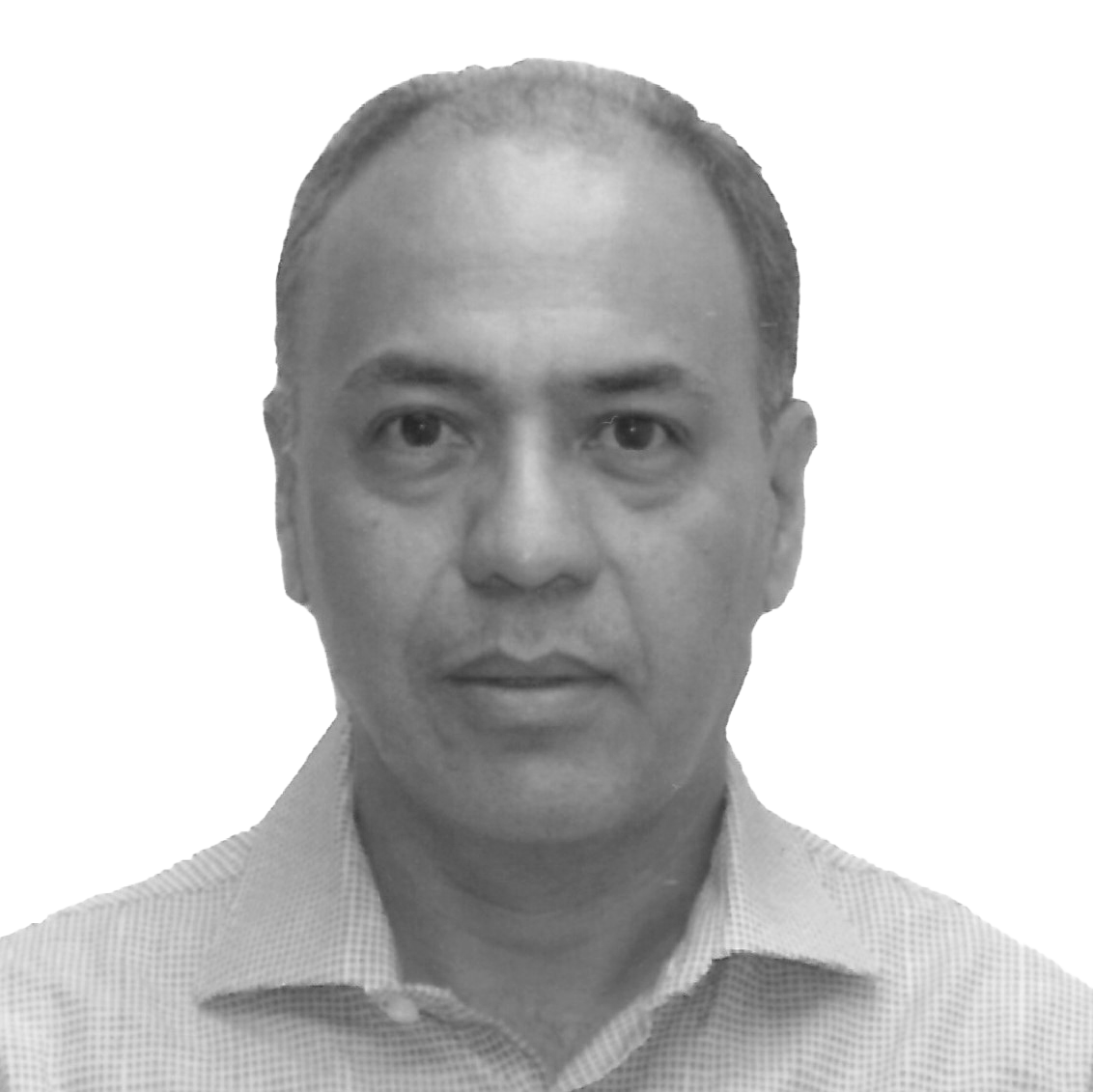
AUTOR:
NICOLAS PALERMO, Ing.
Cuenta con más de 30 años de experiencia. Especialista en Confiabilidad Integral de Activos en PMM Group.